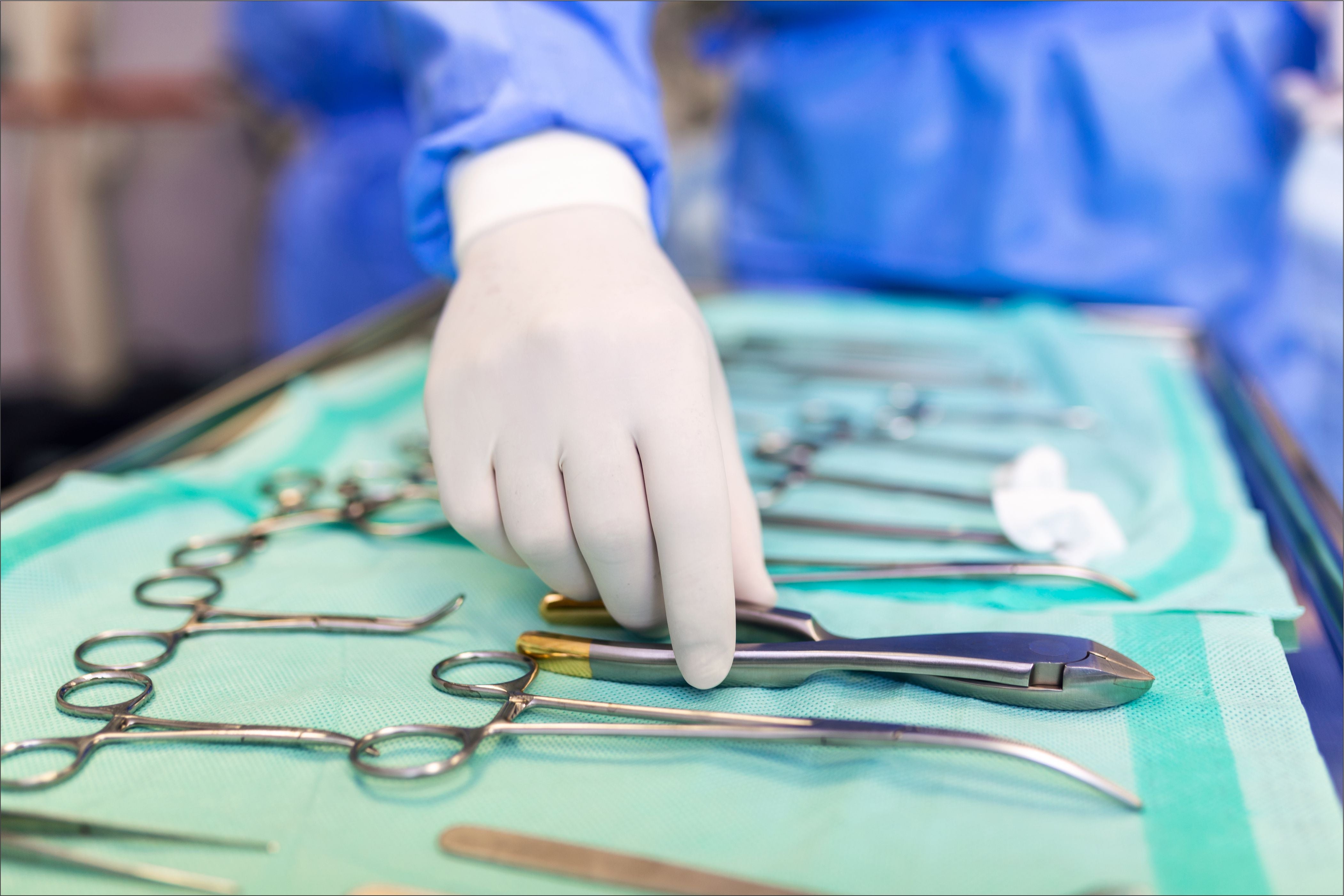
Guide to Maintaining and Cleaning Surgical Instruments
Proper maintenance and cleaning of surgical instruments is essential for ensuring accuracy and safety in any surgical procedure. This guide will provide you with all the necessary information about how to maintain and clean your surgical instruments, as well as advice from qualified experts.
Guide to Maintaining and Cleaning Surgical Instruments as per the recommendations of Ameri Surgicals
Surgical instruments are essential tools used in surgical procedures to help healthcare professionals perform their tasks efficiently and effectively. To ensure that these instruments remain in top condition and continue to function optimally, proper cleaning and maintenance are essential. In this guide, we'll cover the steps required to maintain and clean surgical instruments properly.
Step 1: Pre-Cleaning Inspection
Before cleaning the instruments, it's crucial to inspect them for any visible signs of damage or wear and tear. This inspection should be done immediately after the procedure and should involve examining each instrument individually for any damage such as rust, pitting, or other signs of wear. Instruments with visible damage should be sent for repair or replaced if necessary.
Step 2: Manual Cleaning
After inspection, the instruments must be manually cleaned to remove any residual tissue, blood, or other contaminants. The cleaning process should be done under running water, using a soft-bristled brush to scrub the surface of the instrument. Pay attention to any crevices, hinges, or other hard-to-reach areas to ensure that all contaminants are removed.
It's essential to use a cleaning solution that is designed for surgical instruments. Avoid using harsh chemicals or abrasive cleaning agents, as they can cause damage to the instruments. The cleaning solution should be diluted according to the manufacturer's instructions and should be changed regularly to avoid cross-contamination.
Step 3: Ultrasonic Cleaning
After manual cleaning, the instruments should be placed in an ultrasonic cleaner. Ultrasonic cleaning uses high-frequency sound waves to remove any remaining contaminants, including bacteria, viruses, and other microorganisms. This process is particularly effective in cleaning complex instruments with many crevices and hard-to-reach areas.
When using an ultrasonic cleaner, ensure that the instrument is fully immersed in the cleaning solution and that it is not in contact with any other instrument to avoid damage or cross-contamination. The cleaning time and temperature should be set according to the manufacturer's instructions.
Step 4: Drying and Sterilization
After cleaning, the instruments should be thoroughly dried to prevent corrosion and the growth of microorganisms. Use a lint-free cloth to dry each instrument individually, paying attention to any hard-to-reach areas.
After drying, the instruments should be sterilized to ensure that they are free from any remaining microorganisms. Sterilization can be achieved using various methods, including autoclaving, chemical sterilization, or gas sterilization.
Step 5: Storage
Once sterilized, the instruments should be stored properly to maintain their cleanliness and functionality. The storage area should be dry, clean, and free from any dust or debris. Instruments should be stored in a way that prevents them from coming into contact with other instruments to avoid damage or cross-contamination.
In conclusion, maintaining and cleaning surgical instruments is essential to ensure their longevity and optimal function. The process involves a series of steps, including pre-cleaning inspection, manual cleaning, ultrasonic cleaning, drying and sterilization, and proper storage. Adhering to these steps will help to ensure that surgical instruments are clean, sterile, and ready for use when needed.
Understand the basics of equipment cleaning and maintenance
Before you begin to clean and maintain your surgical instruments, it is important to understand the basics. Cleaning instruments typically involves removing dirt and debris, rinsing off any residue, disinfecting with an appropriate sanitizer or sterilizing a solution, and then drying them off prior to storage. Regular maintenance of your surgical instruments should include lubrication and periodic examination for signs of wear or damage. Following these steps will ensure that your equipment remains in proper working condition and can be used safely during every procedure.
Disassemble surgical instruments for cleaning
Disassembling surgical instruments is necessary for proper cleaning. Carefully take apart your instruments, separating the movable parts and handling portions of the instrument if possible. Some instruments may consist of multiple pieces that must be removed in order to properly clean each part. Use caution when disassembling your instruments to make sure nothing gets damaged or lost. Also, take note of the exact placement of pieces, since incorrect assembly can lead to mistakes during operations.
Use the Correct Temperature and Detergent to Clean Instruments
It is important to use the right amount of detergent and warm water during cleaning. Detergents with pH values between 7 and 8 are best for cleaning surgical instruments. The solution should not be hotter than 122 degrees Fahrenheit, as this could damage your instruments. If any debris remains on the instruments after scrubbing, submerge them in a sterilizing disinfectant or ultrasound cleaner for a few minutes before drying them off.
Carefully lubricate moving parts after cleaning and drying
It is essential to apply lubricant to all small moving parts of the surgical instruments after they have been scrubbed, disinfected, and dried. Using a preferred lubricant, carefully apply it to each part. This will help reduce any future wear and tear that can lead to the device malfunctioning. Be careful not to use too much, as excess lubrication can attract dirt and debris.
Check the equipment for any damage before use.
Make a habit of checking your equipment for damage or wear before you use it. Doing this is a great way to detect any malfunctioning parts and make sure they are still in proper working order. If it’s necessary, keep a special log where you can record the condition of each instrument before you use it, and make sure to check that log every day before you begin work.
Maintaining and cleaning Surgical Instruments FAQs
What are some general rules to follow when cleaning and caring for surgical instruments?
- Always clean the instruments immediately after use to prevent blood, tissue, and other substances from drying and becoming difficult to remove.
- Use only recommended cleaning solutions and tools, and follow the manufacturer's instructions.
- Never use abrasive materials or steel wool to clean the instruments as they can scratch and damage the surface.
- After cleaning, rinse the instruments thoroughly to remove any remaining debris and cleaning solution.
- Dry the instruments with a lint-free cloth to prevent water spots and corrosion.
- Inspect the instruments for any signs of damage, wear, or malfunction before sterilizing them.
- Store the instruments in a dry and clean environment, and avoid exposure to extreme temperatures and humidity.
What guidelines should be followed when cleaning equipment?
- Read the manufacturer's instructions carefully before cleaning the equipment.
- Disassemble the equipment if necessary and clean all parts separately.
- Use only approved cleaning solutions and tools, and follow the recommended dilution and soaking times.
- Rinse the equipment thoroughly with water to remove any remaining debris and cleaning solution.
- Dry the equipment completely before using it or storing it.
- Inspect the equipment for any signs of damage, wear, or malfunction before using it again.
- Store the equipment in a clean and dry environment, protected from dust, moisture, and other contaminants.
How do you maintain surgical instruments?
- Follow the manufacturer's instructions for use and care.
- Clean the instruments after each use and inspect them for any damage or wear.
- Lubricate the moving parts of the instruments regularly to prevent rust and corrosion.
- Sharpen the cutting edges of the instruments as needed to maintain their performance.
- Store the instruments in a clean and dry environment, protected from dust, moisture, and other contaminants.
- Keep a record of the maintenance and repairs performed on each instrument.
What are the various inspections needed to ensure proper working order of surgical instruments?
- Visual inspection: Check the instruments for any signs of damage, wear, or corrosion.
- Functional inspection: Test the instruments to ensure that they perform as expected.
- Sharpness inspection: Check the cutting edges of the instruments to ensure they are sharp and effective.
- Lubrication inspection: Ensure that the moving parts of the instruments are properly lubricated to prevent rust and corrosion.
- Sterilization inspection: Verify that the instruments have been properly sterilized and are ready for use.
What is an equipment inspection checklist?
An equipment inspection checklist is a document that lists the steps and criteria for inspecting a piece of equipment to ensure that it is in good working order. It typically includes the following information:
- Equipment identification information
- Visual inspection items (e.g., cracks, scratches, wear, corrosion)
- Functional inspection items (e.g., power on/off, speed, accuracy)
- Lubrication inspection items (e.g., oil level, grease fittings)
- Sharpness inspection items (e.g., cutting edges, blades)
- Sterilization inspection items (e.g., date of last sterilization, sterilization method)
- The checklist is used by technicians and other personnel responsible for maintaining and inspecting the equipment to ensure that it is properly maintained and ready for use.
What are the 5 types of OSHA inspections?
The five types of OSHA inspections are:
- programmed inspections, which are scheduled based on an employer's industry and injury rates;
- complaint inspections, which are initiated based on an employee complaint or referral;
- referral inspections, which are initiated by other agencies or organizations;
- follow-up inspections, which are conducted to ensure that previously cited violations have been corrected; and
- imminent danger inspections, which are conducted when OSHA believes there is a risk of death or serious physical harm.
What does JHA stand for?
JHA stands for Job Hazard Analysis. It is a process that identifies potential hazards in a workplace and assesses the risks associated with those hazards. JHAs are typically conducted before new work processes or equipment are introduced, and they are used to develop safety procedures and protocols.
What are the three main steps of an OSHA inspection?
The three main steps of an OSHA inspection are:
- opening conference, where the OSHA inspector explains the purpose and scope of the inspection, reviews the employer's injury and illness records, and requests a tour of the workplace;
- walkthrough, where the OSHA inspector conducts a physical inspection of the workplace, identifies potential hazards, and interviews employees; and
- closing conference, where the OSHA inspector discusses any violations found during the inspection, explains the potential consequences of those violations, and provides a timeline for correcting the violations.
What are the 4 priorities of OSHA inspection?
The four priorities of OSHA inspection are:
- imminent danger situations, where there is a risk of death or serious physical harm;
- fatalities and catastrophes, where a workplace incident has resulted in a death or hospitalization of three or more employees;
- employee complaints, where OSHA has received a complaint from an employee or their representative about a workplace hazard; and
- programmed inspections, which are based on an employer's industry and injury rates. OSHA may also conduct inspections in response to referrals from other agencies or organizations, or to follow up on previously cited violations.
30 comments
-
Зарегистрироваться на сайте:
- Перейдите на официальный сайт “Калино Вулкан”.
- Нажмите на кнопку “Регистрация” или “Зарегистрироваться”.
- Заполните все необходимые поля, включая имя, адрес электронной почты и пароль.
- Подтвердите регистрацию, следуя инструкциям на экране.csaefe
-
Зарегистрироваться на сайте:
- Перейдите на официальный сайт “Калино Вулкан”.
- Нажмите на кнопку “Регистрация” или “Зарегистрироваться”.
- Заполните все необходимые поля, включая имя, адрес электронной почты и пароль.
- Подтвердите регистрацию, следуя инструкциям на экране.csaefe
-
Зарегистрироваться на сайте:
- Перейдите на официальный сайт “Калино Вулкан”.
- Нажмите на кнопку “Регистрация” или “Зарегистрироваться”.
- Заполните все необходимые поля, включая имя, адрес электронной почты и пароль.
- Подтвердите регистрацию, следуя инструкциям на экране.csaefe
-
Зарегистрироваться на сайте:
- Перейдите на официальный сайт “Калино Вулкан”.
- Нажмите на кнопку “Регистрация” или “Зарегистрироваться”.
- Заполните все необходимые поля, включая имя, адрес электронной почты и пароль.
- Подтвердите регистрацию, следуя инструкциям на экране.csaefe
Robertflier
Зарегистрироваться на сайте:
- Перейдите на официальный сайт “Калино Вулкан”.
- Нажмите на кнопку “Регистрация” или “Зарегистрироваться”.
- Заполните все необходимые поля, включая имя, адрес электронной почты и пароль.
- Подтвердите регистрацию, следуя инструкциям на экране.
csaefe